Stand der Technik: Die in Deutschland bekannteste technische Regel zur Beurteilung der Korrosionsgefährdung von Heizanlagen ist die VDI 2035-2. Sie befindet sich in der Überarbeitung, eine aktualisierte Version liegt bereits im Entwurf vor. Daneben gibt es noch die Europäische Norm DIN EN 14 868 als Leitfaden für die Ermittlung der Korrosionswahrscheinlichkeit in geschlossenen Wasserzirkulationssystemen < 110 °C (also auch Kühl- und Kältesysteme), die es ebenfalls zu beachten gilt. Die VDI 2035 geht allerdings ausdrücklich von korrosionstechnisch geschlossenen Systemen aus, in denen es also keinen signifikanten Sauerstoffeintrag gibt, während die Europäische Norm zusätzlich auch Anlagen mit Sauerstoffzutritt in die Betrachtung einbezieht.
Wie gelangt Sauerstoff ins Heiz- und Kühlsystem?
In den betrachteten Heiz- und Kühlsystemen werden die Korrosionsprozesse im Wesentlichen durch die Menge des eindringenden Sauerstoffs bestimmt, solange sich die pH-Werte des Kreislaufwassers im Bereich von 8 bis 9 bewegen. Grundsätzlich ist die chemische Reduktion eines Oxidationsmittels, wie z. B. Sauerstoff, notwendig, damit der Auflösungsprozess desselben am metallischen Werkstoff ungehindert weiter fortschreiten kann, ohne den Werkstoff selbst zu beeinträchtigen. Auch Säuren – erkennbar am niedrigen pH-Wert des Kreislaufwassers – erfüllen diese Voraussetzung. Die mögliche Geschwindigkeit dieses Korrosionsprozesses hängt aber noch von anderen Wasserparametern ab, aber mehr dazu später im Beitrag.
Sauerstoff kann auf verschiedenen Wegen in ein Heiz- oder Kühlsystem eingebracht werden:
T > 40 °C)
Die Korrosionsrate bleibt in der Theorie vernachlässigbar gering, wenn der im Füllwasser vorhandene natürliche Sauerstoffgehalt durch Korrosionsprozesse verbraucht ist, wenn über die Lebensdauer der Anlage nicht mehr als deren doppeltes Anlagenvolumen nachgespeist wird und Sauerstoffzutritt nicht nennenswert möglich ist. Bei großen, verzweigten Anlagen ist dies aber in der Praxis kaum zu realisieren.
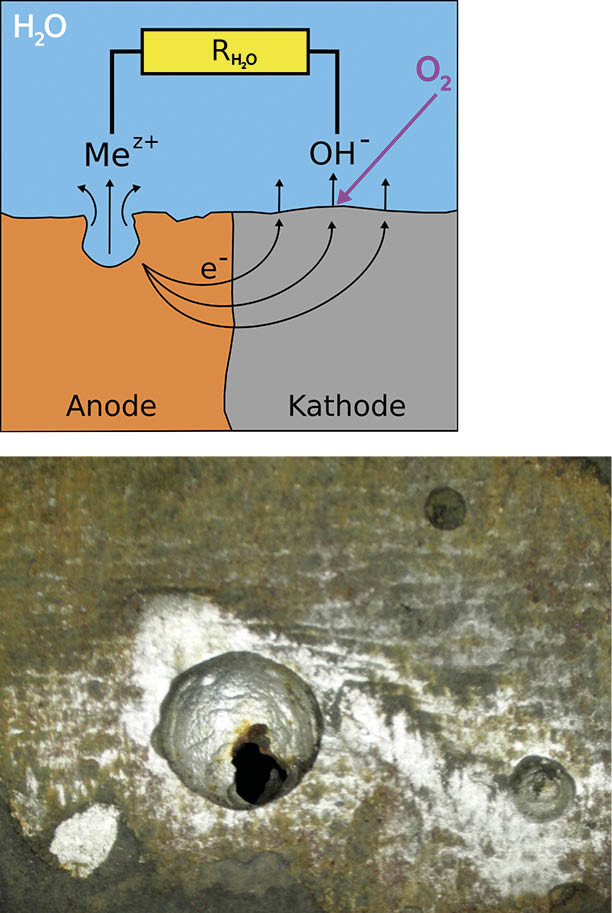
Bild: permatrade
Salzarme Betriebsweise nach VDI 2035
Grundsätzlich hat Schwarzstahl die Tendenz, sich in wässriger Umgebung (gemäß Fe → Fe2+ + 2e-) aufzulösen, wie in Bild1 schematisch gezeigt. Die am Metall zurückbleibende Ladung (e-) wird in unmittelbarer Nähe zur Austrittstelle einem Oxidationsmittel – in der Regel im Wasser gelöstem Sauerstoff – angeboten, wobei sich Hydroxidionen gemäß ½O2 + 2e- + H2O → 2OH- bilden. Der „elektrische“ Ladungsausgleich geht dabei über das Wasser und steht in direkter Beziehung zu dessen elektrischer Leitfähigkeit. Eine niedrige Leitfähigkeit, wie sie bei salzarmer Betriebsweise gegeben ist, begrenzt die Korrosionsgeschwindigkeit deutlich, kann aber letztlich auch nicht vor Sauerstoffkorrosion schützen.
Werkstoffe aus Aluminiumlegierungen sind hinsichtlich Sauerstoffkorrosion deutlich weniger empfindlich, da sich dieser Werkstoff im sauerstoffhaltigen Wasser sehr gut passivieren kann. Sind allerdings Chloridionen in höherer Konzentration vorhanden, kann es trotzdem zu Lochkorrosion und Wanddurchbrüchen kommen. Dies gilt mehr oder weniger auch für molybdänfreie nichtrostende Stähle. Bei einer salzarmen Betriebsweise nach VDI 2035 (LF < 100 µS/cm) werden diese kritischen Chloridkonzentrationen jedoch nie erreicht.
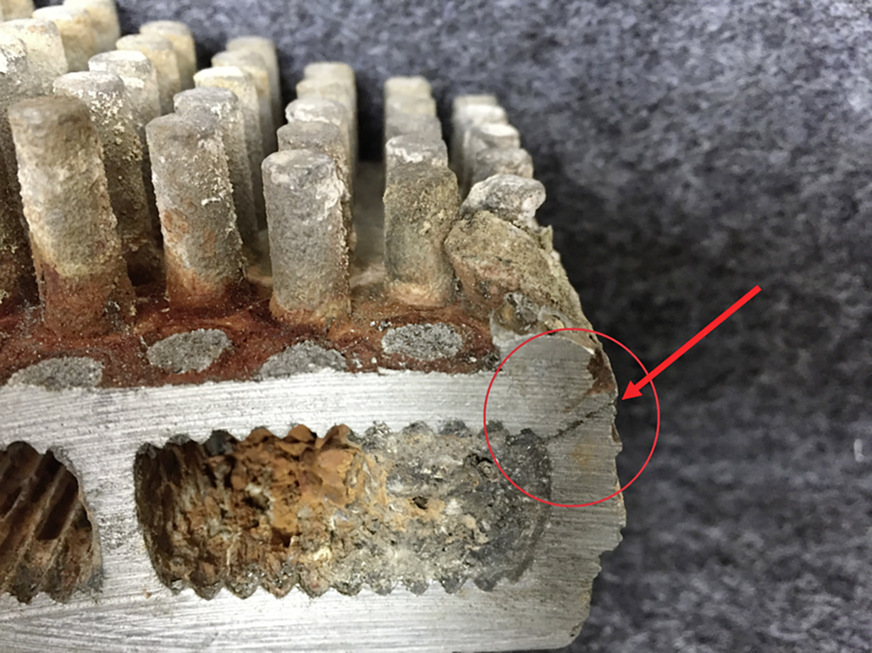
Bild: permatrade
Aber selbst wenn für einen Werkstoff alle Wasserparameter passen, kann dieser trotzdem durch sedimentierende Stoffe, z. B. durch Korrosionsprodukte anderer Werkstoffe, so geschädigt werden, dass ein Schaden eintritt, siehe Bild 2.
pH-Wert und Leitfähigkeit
Das Ausmaß sowie die Geschwindigkeit einer möglichen Sauerstoffkorrosionserscheinung hängen von mehreren Einflussfaktoren ab. Primärer Faktor ist natürlich die Konzentration an gelöstem Sauerstoff im Kreislaufwasser, aber auch die Parameter Härte, pH-Wert und Leitfähigkeit spielen eine Rolle. Dies soll nachfolgend etwas detaillierter beleuchtet werden.
Grenzwerte nach VDI 2035 und AGFW FW 510
Nicht speziell entgastes oder sauerstoffgezehrtes Füllwasser enthält 8 bis 11 g/m³ gelösten Sauerstoff. Bei der Reaktion mit Bauteilen aus Schwarzstahl bildet sich dadurch letztlich Magnetit (je m³ ca. 36 g), gleichzeitig sinkt die Sauerstoffkonzentration auf Werte < 0,1 mg/l ab.
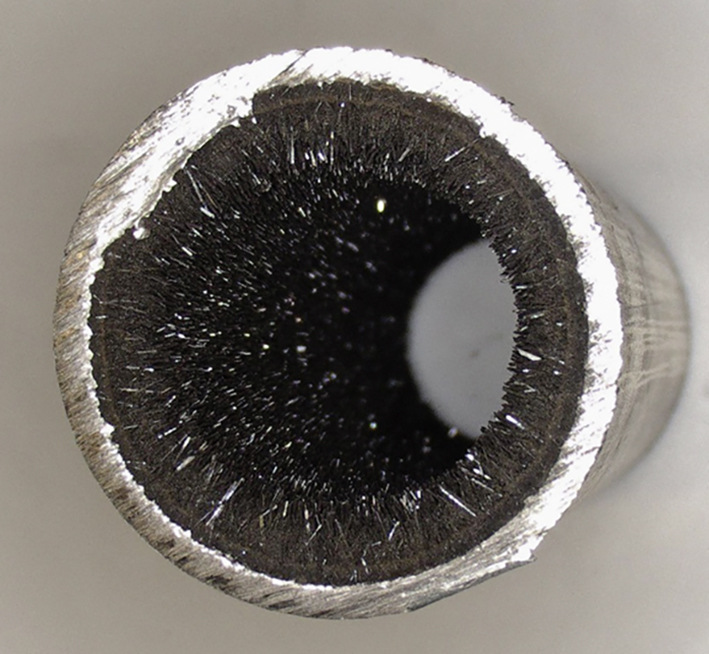
Bild: permatrade
In der Praxis werden bei korrosionstechnisch geschlossenen Anlagen Werte von 0,03 bis 0,1 mg/l gemessen. Die VDI 2035 nennt hier einen Grenzwert von 0,1 mg/l, unterhalb dessen keine Schäden zu erwarten sind. Für direkt an die Fernwärme angeschlossene Anlagen sind nach AGFW FW 510 aber strengere Vorgaben (0,02 bis 0,1 mg/l) zu beachten.
Dem Korrosionsmodell von Bild 1 entsprechend kann eine höhere Sauerstoffkonzentration auch mehr elektrische Ladung (e-) übernehmen, die von den austretenden positiven Eisenionen beim Übertritt ins Heizungswasser am Metall zurückgelassen werden. Diese Depolarisation stellt eine Voraussetzung für den ungehinderten Auflösungsvorgang des metallenen Festkörpers dar. Letztlich führt dies zu einem Versagen des Bauteils oder zumindest zu einer übermäßigen Bildung von Magnetit, siehe Bild 3. Fehlt der Sauerstoff, kommt dieser Korrosionsprozess zum Stillstand.
Elektrische Leitfähigkeit des Heizungswassers
Beim Korrosionsvorgang nach Bild 1 treten sowohl positive Fe2+- als auch negative OH--Ionen in das Wasser über. Deren elektrischer Ladungsausgleich erfolgt über das Wasser und wird von einer zunehmenden Wasserleitfähigkeit begünstigt. Niedrige Leitfähigkeiten behindern neben diesem auch alle anderen elektrochemischen Vorgänge an der Metalloberfläche.
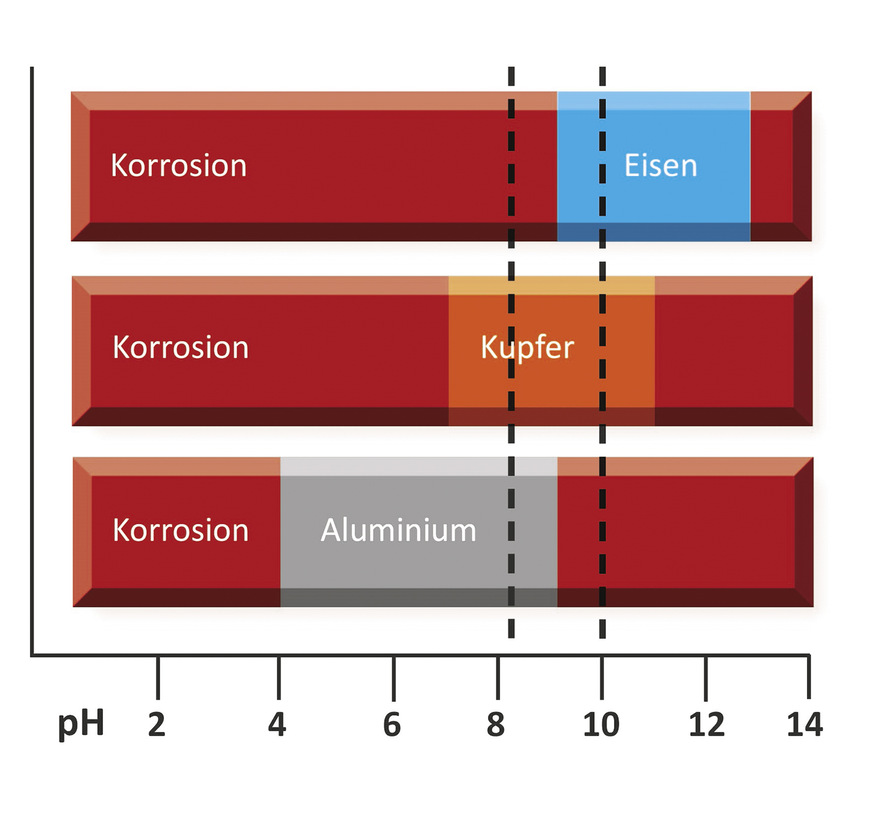
Bild: permatrade
pH-Wert des Heizungswassers
Zunächst entscheidet der pH-Wert darüber, ob sich auf dem Metall eine Deckschicht ausbilden kann oder nicht. In Bild 4 sind die pH-Bereiche für die Werkstoffe Eisen, Kupfer und Aluminium dargestellt, bei denen sich eine sog. Passivschicht aus Korrosionsprodukten bildet, die zumindest die weitere Flächenkorrosion massiv eindämmt. Als bestmöglichen Kompromiss für die im Heizkreis verbauten Metalle fordern die einschlägigen Regelwerke, insbesondere die VDI 2035, einen pH-Bereich von 8,2 bis 9,0. Für Anlagen ohne Aluminiumkomponenten sollte der pH-Wert jedoch zwischen 9,3 und 10,0 gewählt werden, nicht nur wegen des passiven Verhaltens des Eisens, sondern auch deshalb, weil die Reduktion des Sauerstoffs an der Metalloberfläche vom pH-Wert abhängig ist und bei niedrigeren pH-Werten leichter abläuft. Hinzu kommt noch, dass bei pH-Werten < 6,0 zunehmend die Säurekorrosion in Aktion tritt und die H+-Ionen den Sauerstoff als Oxidationsmittel abzulösen beginnen. Derart niedrige pH-Werte sind bei verschleppten, zu Säuren degradierten Frostschutzmittelresten im Heizungswasser keine Seltenheit.
Wassserhärte des Heizungwassers
Etwas Resthärte im Heizungswasser wirkt sich grundsätzlich positiv aus, was die Sauerstoffkorrosion betrifft. Dies rührt daher, dass die Reduktion von Sauerstoff die Metalloberfläche alkalisiert (Bildung von OH-, s. o.), wodurch dort Kohlensäure gebunden wird. Befindet sich gelöster Kalk im Wasser, wird dieser sich an der alkalisierten Metalloberfläche abscheiden und so die weitere Reaktion behindern oder, in anderen Worten: inhibieren. Signifikant ist dieser Effekt vor allem bei neutralen Wässern. Korrosionschemisch betrachtet wirkt Kalziumkarbonat hier als sogenannter kathodischer Korrosionsinhibitor. Nicht erwähnt werden muss, dass es hier im Gegensatz zu anodisch wirkenden Inhibitoren – bei einer möglichen Unterdosierung – zu keiner erhöhten lokalen Korrosionserscheinung kommt.
In der Zusammenfassung bedeutet dies, dass eine salzarme Betriebsweise mit möglichst hohem pH-Wert wasserseitig zwar den bestmöglichen Korrosionsschutz darstellt, aber für die Fälle eines nennenswerten Sauerstoffeintrags keinen wirklichen Schutz bietet. Lässt sich ein Sauerstoffeintrag nicht durch andere technische Maßnahmen, z. B. mittels Systemtrennung, beherrschen, kann die direkte Sauerstoffbindung oder auch der Einsatz von Korrosionsinhibitoren im Heizwasser erwogen werden. Möglichkeiten der Sauerstoffbindung sind:
Außerdem gibt es ein neues physikalisch-chemisches Verfahren, dazu später mehr. Bevor wir die Möglichkeiten der Sauerstoffbindung näher beleuchten, ein paar Sätze zu den sogenannten Vollschutzprodukten, die auch in korrosionstechnisch offenen Systemen zum Einsatz kommen.
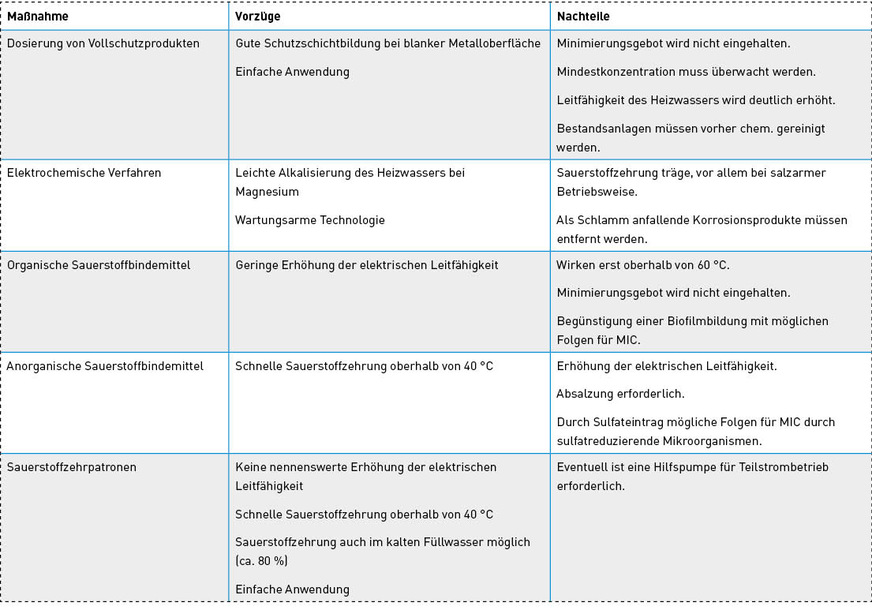
Quelle: permatrade
Vollschutzprodukte gegen Korrosionsschäden
Produkte dieser Art enthalten meist auch anodisch wirkende Korrosionsinhibitoren, die in der Wirkstoffkonzentration – in der Regel jährlich – zwingend überprüft werden müssen und mehr oder weniger nur auf blanken Metalloberflächen messtechnisch schöne Ergebnisse von Schutzschichten zeigen. Deshalb wird auch eine vorhergehende chemische Reinigung vom Hersteller gefordert. Benzotriazole, eine häufig verwendete Substanzgruppe, zeigen beispielsweise eine hohe Mobilität im Boden, werden von der Kläranlage nur unzureichend entfernt und gelangen so in die aquatische Umwelt (laut Grundwasserdatenbank Wasserversorgung, 23. Jahresbericht 2014).
Gilt das Produkt als biologisch abbaubar, dient es nebenbei noch als Nahrung für Mikroorganismen, die nicht nur isolierende Biofilme bilden, sondern unter Umständen Sulfat zu stark korrosiv wirkendem Sulfid reduzieren können. Dem wiederum wird oft mit einem Biozidzusatz begegnet. Das Minimierungsgebot (so wenig Einsatz von Chemie wie möglich) wird hierbei komplett übergangen.
Elektrochemische Verfahren zur Sauerstoffbindung
Die elektrochemischen Verfahren zur Sauerstoffbindung nutzen ein „unedles“ Metall – in der Regel eine Magnesiumlegierung – im galvanischen Kurzschluss, mit einem Bauteil aus Edelstahl kurzgeschlossen. Während sich das Magnesium auflöst, findet parallel dazu an der Edelstahloberfläche die elektrochemische Reduktion von Sauerstoff statt. In der Summe entsteht dann Magnesiumhydroxid als Korrosionsprodukt, das als Schlamm entfernt werden muss. Gleichzeitig wird der pH-Wert etwas angehoben. So weit, so gut, wäre da nicht die Sauerstoffbindegeschwindigkeit recht niedrig und das Gerät auch eher für den Hauptstrom auszulegen. Wird die Anlage salzarm betrieben, ist der Einsatz zu hinterfragen. Entgegen anderslautenden Aussagen empfiehlt die VDI 2035 den Einsatz dieser Geräte nicht explizit als technisch gute Lösung zur Sauerstoffbindung.
Chemische Verfahren zur Sauerstoffbindung
Für die chemische Bindung von Sauerstoff wird meist Natriumsulfit dazudosiert, das ab Temperaturen von ca. 40 °C eine hohe Sauerstoffbindegeschwindigkeit zeigt. Organische Bindemittel wirken erst oberhalb von 60 °C, fördern die Biofilmbildung und erhöhen so die Wahrscheinlichkeit für mikrobiell induzierte Korrosionserscheinungen. Die VDI 2035 rät daher – in ihrem Gültigkeitsbereich – zum Verzicht.
Aber auch Natriumsulfit zeigt Nebenwirkungen. Bei der Reaktion mit Sauerstoff entsteht Sulfat, das die Leitfähigkeit des Heizwassers im Laufe der Zeit stark erhöht. In der Anlagenpraxis finden sich hier nicht selten Werte bis 2000 µS/cm, was gelegentlich Ausblühungen (Salzkrusten) an Regelventilen verursacht. Zudem besteht v. a. im Niedertemperaturbereich auch wieder eine erhöhte Wahrscheinlichkeit, dass sulfatreduzierende Mikroorganismen korrosiv wirkendes Sulfid erzeugen.
Physikalisch-chemisches Verfahren zur Sauerstoffbindung
Zum neuen physikalisch-chemischen Verfahren: Bei dieser Art von „Filterpatrone“ kann der im Wasser gelöste Sauerstoff direkt beim Hindurchströmen eliminiert werden. Der Prozess ist allerdings von der Wassertemperatur abhängig. Wird eine Heizanlage mit kaltem Wasser über eine solche Patrone – ggf. in Kombination mit einer Entsalzung oder Enthärtung – neu befüllt, können dem Füllwasser direkt 80 % Sauerstoff entzogen werden. Logischerweise bilden sich dann auch 80 % weniger Korrosionsprodukte, die z. B. die Topmeter von Fußbodenheizungsverteilern belegen könnten. Dabei ist es unerheblich, ob die Sauerstoffzehrpatrone vor oder hinter der Aufbereitungseinheit platziert wird.
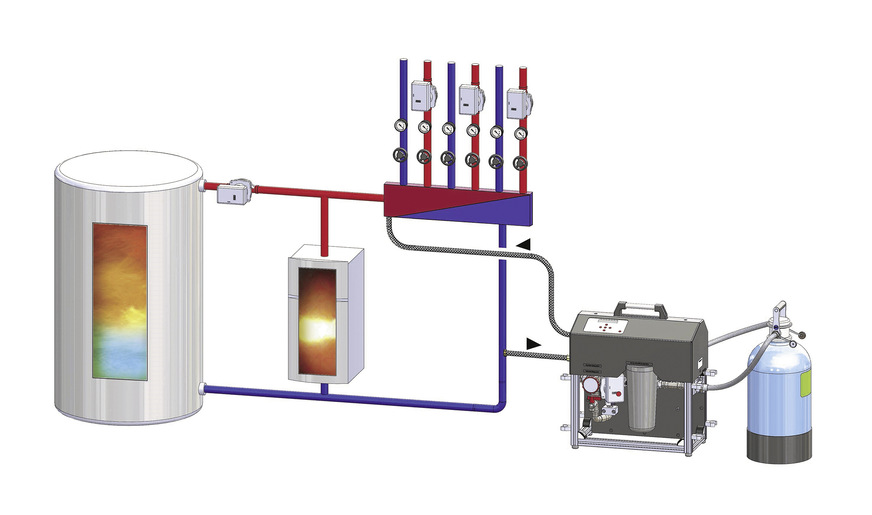
Bild: permatrade
Prädestiniert für dieses Filterverfahren ist die Anwendung während des Heizbetriebs im Teilstrom, wobei bereits ab einer Wassertemperatur von 40 °C der Sauerstoff mit hoher Geschwindigkeit auf eine Restkonzentration von < 0,02 mg/l gezehrt wird. Im einfachsten Fall kann mittels Edelstahlwellrohren und eines sog. Tacosetters eine solche Filterpatrone zwischen Rücklauf und Vorlauf (saugseitig!) installiert werden. Technisch eleganter ist die Lösung in Kombination mit einem fest installierten Modul zur Teilstromentsalzung, siehe Bild 5. Hier kann das Wasser entweder ständig oder zeitgesteuert mechanisch filtriert und vom Restsauerstoff befreit werden. Falls erforderlich, lässt sich zudem eine Entsalzungspatrone in Abhängigkeit der Leitfähigkeit des Anlagenwassers automatisch hinzuschalten.
Literaturempfehlung:
TIPP
Sauerstoffmessung im Heizungswasser
Um es gleich vorwegzunehmen: Das Heizwasser muss direkt beim Ausströmen an der Anlage bei einer Temperatur < 50 °C gemessen werden. Eine Probenahme für ein Labor oder die Messung in einem Gefäß bringt hier ansonsten nur falsche, deutlich zu hohe Werte. Auch sollte vorzugsweise eine optische Messsonde eingesetzt werden, da diese schnell anspricht und mit sehr niedrigen Sauerstoffkonzentrationen zurechtkommt. Die Vorgehensweise:
Die Messung der gelösten Sauerstoffkonzentration gibt zwar eine wichtige Auskunft, ist aber mehr oder weniger eine Momentaufnahme und hängt oft noch vom Messort in der Anlage ab. Entsprechend dem Entwurf der neuen VDI 2035 sollte die Konzentration des gelösten Sauerstoffs < 0,1 mg/l betragen (Richtwert), damit die Korrosionswahrscheinlichkeit für die in Fließrichtung nachfolgenden Bauteile gering bleibt.
Dieser Beitrag ist eine Überarbeitung des Artikels „Wir müssen draußen bleiben“ von Dr. Dietmar Ende aus SBZ 08-2020.